本文
「知の拠点」重点研究プロジェクトにおいて微粒子ピーニング装置を開発しました
平成25年2月20日(水曜日)発表
― CFRPの加工や刃物の長寿命化を実現 ―
愛知県が公益財団法人科学技術交流財団に委託して実施している共同研究開発「重点研究プロジェクト(※1)」の「低環境負荷型次世代ナノ・マイクロ加工技術(※2)の開発プロジェクト(※3)」において、名城大学(理工学部材料機能工学科 宇佐美初彦(うさみはつひこ)教授)、伊藤機工株式会社、IKKショット株式会社は共同で投射粒子に極微細粒子を用いる微粒子ピーニング(※4)装置を開発しました。
この装置の大きな特徴は、直径10μm程度の極微細粒子を凝集することなく投射でき、さらに投射する極微細粒子の速度と流量を個別に制御できることです。
この装置を用いて粒子の投射条件を最適化することで、次世代自動車や航空機の材料として利用が期待される炭素繊維強化プラスチック(CFRP)やセラミックスの高速穴あけ加工、工具刃先のような硬くて脆い素材に対する耐久性の改善、さらには、薄く柔らかい素材である紙面の文字や図を選択的に“削り落とす”ことなどが可能となります。
今後、この微粒子ピーニングを、CFRPの加工、工具の長寿命化のみならず、摩擦低減や高い耐摩耗性を実現する表面処理技術へ適用していきます。
1 開発の背景
ショットピーニングとは、冷間加工(※5)の一種であり、粒径1mm程度の鉄やガラス等の粒子を高速度で鋼(はがね)表面に衝突させることで、鋼の投射面に圧縮の残留応力(※6)を付与する表面処理技術です。これまで、この技術は主にばねや歯車などの機械部品に対し、疲労強度特性の改善を目的として使用されてきました。しかし、粒子が衝突した投射面が荒れるため、その適用には限界がありました。
この課題を解決するため、微細化した粒子を金属表面に衝突させる「微粒子ピーニング」が考案され、材料表面の粗さを低減することが可能となりました。
しかし、微粒子が小さくなることで、新たな次の3つの大きな課題が生じ、実用化の壁となっていました。
(1) 吹き付ける微粒子が凝集しやすく大きな塊になってしまうこと。
(2) 微粒子にエネルギーを付与するためには、高速度で粒子を投射する必要がある。しかし、粒子の速度と流量をそれぞれ個別で調整することは難しく、高速投射をするには、必然的に大流量となってしまう。
(3) 工具刃先に使用される超硬合金や硬質薄膜は硬くて脆いので、投射条件を精密に制御しないと表面が損傷する可能性が高い。
そこで、これらの課題を解決するため、「重点研究プロジェクト」において、名城大学(理工学部材料機能工学科 宇佐美初彦(うさみはつひこ)教授)、伊藤機工株式会社、IKKショット株式会社は共同研究に取り組み、微細粒子が凝集しにくく、粒子の速度と流量を個別に調整することができる微粒子ピーニング技術を開発しました。
2 開発の内容
開発した試作装置の概要及び特徴を以下に示します。
概要
開発した試作装置には下記の2つの特徴があり、その概略図を図1に示します。
(1)粒子の凝集を避けるため、ゴムボールを内蔵した粒子タンク。
(2)粒子の速度と流量を個別に調整するため、同心円2重管構造を持つ投射ノズルで粒子を噴射。
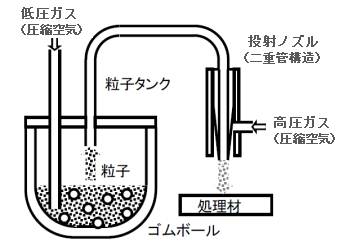
図1 開発した装置の概略図
ゴムボールを内蔵した粒子タンク内で、底面より圧縮空気を導入することで、粒子は上部に噴き上げられ、2重管構造を持つ投射ノズルへ入っていきます。この時、ゴムボールがタンク内で運動することにより、粒子を撹拌し、微細粒子の凝集を妨げます(図2に微細粒子の例を示します)。
2重管構造の外側から高圧ガスを入れることで、2重管構造を持つ投射ノズルの内側から出てきた粒子を加速することができる構造になっています。
ノズルの内側で粒子の流量を、外側から加速用の高圧ガスを導入することで粒子の速度を、それぞれ個別に制御することが可能となりました。
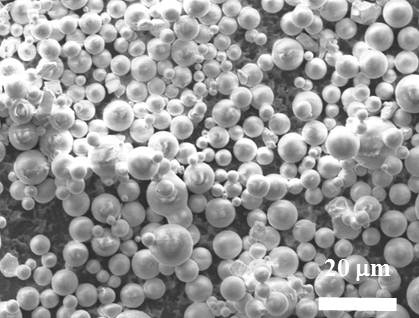
図2 投射可能となった微細粒子
(ガラス粒子:平均粒径10μm以下)
特徴
これまで難しかった粒子流量と粒子速度を個別に制御することができるようになったことで、下記のような表面処理が可能になりました。
○研磨材のような微細砥粒を投射することで、CFRP(図3)や繊維強化多孔質セラミックス(図4)のような加工が難しい「難加工性材料」の穴あけ加工。
○粒径10μm以下の微細粒子の投射によって材料の極表層を選択的に硬質化できるので、コーティング工具の表面特性改善にも適用可能。
○表面に小さな凹面(ディンプル)をつけること、テフロンのような固体潤滑材を転写させることで、潤滑性及び摩擦特性の向上。
微粒子の周囲に微細粉体を吸着(図5)させ投射することで、投射面に微細粉体を転写させ、表面に機能性を付与できます。具体的には固体潤滑材であるテフロン微細粉体を鉄粒子に吸着させて投射することで、投射面の硬質化と低摩擦化を同時に付与できます。
○薄く柔らかい素材である紙面の文字や図を選択的に“削り落とす”こと。
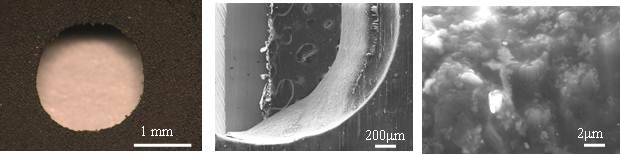
図3 穴あけ加工されたCFRP
(左から 加工穴全体像、加工孔周囲、加工孔周囲拡大像)
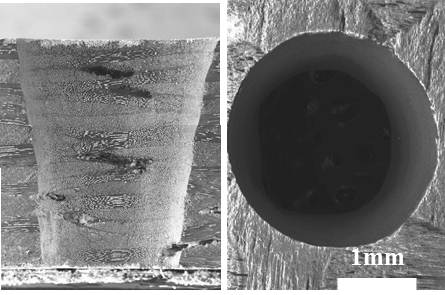
図4 穴あけ加工された繊維強化多孔質セラミックス
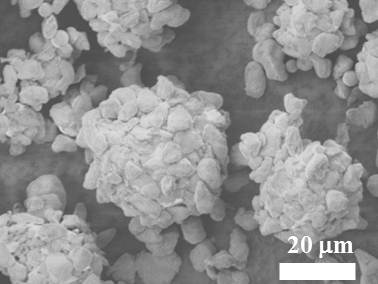
図5 テフロン(PTFE)粉末でコーティングされた粒径50μmの鋼粒子
3 今後の展開
工具刃先に用いられる極めて硬くて脆い材料の表面特性の改善、CFRPの高速切断加工の開発を目的として、微粒子ピーニングの最適条件を検討し、さらなる装置の改良を行っていきます。
5 問合せ先
・プロジェクト全体に関すること
あいち産業科学技術総合センター 企画連携部
(1)担 当:清水、鹿野
(2)所 在 地:豊田市八草町秋合1267番1
(3)電話:0561-76-8306
(4)F A X :0561-76-8309
公益財団法人科学技術交流財団 知の拠点重点研究プロジェクト統括部
(1)担 当:大西、佐藤、石川
(2)所 在 地:豊田市八草町秋合1267番1
(3)電話:0561-76-8360
(4)F A X :0561-21-1653
・本開発の技術内容に関すること
名城大学 理工学部 材料機能工学科
(1)担 当:教授 宇佐美 初彦
(2)所 在 地:名古屋市天白区塩釜口1-501
(3)電話:052-832-1151
(4)F A X :052-832-1235
・本開発の装置に関すること
伊藤機工株式会社
(1)担 当:大河内、伊藤(誠)
(2)所 在 地:東海市南柴田町ヌノ割412番地の4
(3)電話:052-689-2215
(4)F A X:052-689-2218
IKKショット株式会社
(1)担 当:安藤
(2)所 在 地:東海市南柴田町ヌノ割412番地の4
(3)電話:052-604-1215
(4)F A X :052-604-1285
【用語説明】
※1 「知の拠点」重点研究プロジェクト
「知の拠点」は、万博跡地にあり、産学官が連携し共同研究開発を行う「あいち産業科学技術総合センター」とナノテク研究に不可欠な高度計測分析施設である「シンクロトロン光利用施設」からなる。
「知の拠点」重点研究プロジェクトは、大学等のシーズをもとに企業による製品化を図るため、「知の拠点」で行う産学官連携の共同研究開発である。
※2 ナノ・マイクロ加工技術
100万分の1mmであるナノメートル(nm)またはその1000倍のマイクロメートル(μm)単位の精度の加工のこと。3次元構造の微細加工技術では、最小寸法がマイクロレベルの高精度の機械加工が必要で、さらに、表面処理などでは原子レベル(ナノレベル)での改質が求められている。
※3 低環境負荷型次世代ナノ・マイクロ加工技術の開発プロジェクト(概要)
<プロジェクトリーダー>
名古屋工業大学 副学長・教授 中村隆 氏
<内容>
愛知のモノづくりの根幹をなす加工技術において、地域のモノづくりを熟知した素材・加工の研究者が集結し、次世代自動車や航空機に活用が進む新素材に対する高精度・低コストな加工技術を確立する。
<参加機関>
7大学5公的研究機関31企業(うち中小企業16社)(平成24年12月現在)
・うち大学
愛知工業大学、大同大学、豊田工業大学、豊橋技術科学大学、名古屋工業大学、名古屋大学、名城大学
・うち公的研究機関
あいち産業科学技術総合センター、(公財)科学技術交流財団、(独)産業技術総合研究所、(一財)ファインセラミックスセンター、(独)理化学研究所
(注)大学名及び公的研究機関名は、五十音順で掲載。
※4 微粒子ピーニング
極微細粒子を高速度で材料表面に衝突させる(投射する)ことで、材料の表面改質等を行う技術。粒径1mm程度の粒子を投射する一般的なショットピーニングに比べ、投射粒子の径が0.05mm(50μm)程度と小さいことが特徴である。
※5 冷間加工
加熱することなく、材料に力をかけて変形させる加工。
※6 残留応力
材料に外部から力を与えた後、その力を取り除いても材料内に残っている力。一般に、材料は引張の応力で破損するため、圧縮の残留応力があると疲労強度が向上する。
問合せ
あいち産業科学技術総合センター
企画連携部企画室
担当 清水、鹿野
電話 0561-76-8306(ダイヤルイン)
産業労働部産業科学技術課
科学技術グループ
担当 中川、榊原、加藤(英)
内線 3383、3382
電話 052-954-6351(ダイヤルイン)